Joby Aviation, in collaboration with A&P Technology, Toray Advanced Composites, and the National Institute for Aviation Research, conducted a time study seeking to optimize aircraft part design for high production rates, while meeting cost and sustainability targets. The project involved production of a partial wing spar and A&P’s continuous +/-45° braided reinforcements demonstrate improved production rates, cost.
Author: Molly Dingeldein
A&P Technology’s QISO and IDI Composites’ Fortium SMC – BETTER TOGETHER
IDI Composites (Noblesville, IN) partnered with A&P Technology to develop a prepreg co-molding compound known as Fortium QISO – a new class of reinforcement yielding high strength and impact resistance and the ability to mold into complex geometries.
Revolutionizing Composite Manufacturing: A Closer Look at A&P Technology’s QISO
In the ever-evolving world of composite materials, A&P Technology stands out with its innovative QISO® technology. QISO® represents a significant leap forward in composite architecture, offering a triaxially braided structure that distributes material evenly in all directions by weight. This quasi-isotropic design not only enhances dimensional stability but also delivers remarkable benefits in terms of thermal management and structural integrity.
Unleashing the Power of QISO®
QISO®’s triaxial architecture allows each fiber to move independently, enabling the formation of complex shapes without the need for cuts and overlaps. This unique feature not only simplifies the manufacturing process but also ensures more consistent thicknesses and better thermal transfer during cure cycles. Compared to traditional woven structures, QISO® eliminates the complexity of layer-to-layer rotation and the need for balancing laminate stacks, thereby streamlining production and reducing scrap by up to 40%.
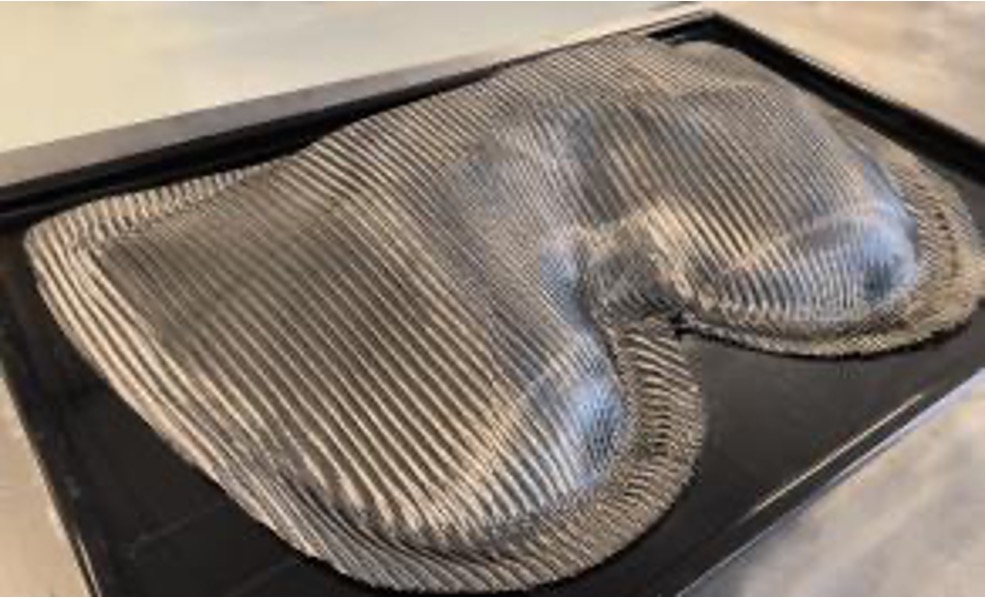
Efficiency Redefined
One of the standout advantages of QISO® is its ability to simplify layups while enhancing drapability. This translates into significant reductions in labor and manufacturing costs, making it a preferred choice for industries where efficiency and cost-effectiveness are paramount. Available in a range of areal weights, from lightweight face sheets to heavier bulk plies, QISO® caters to diverse applications without compromising on performance.
Conclusion
In conclusion, A&P Technology’s QISO® sets a new benchmark in composite material technology. Its innovative design not only meets the rigorous demands of modern manufacturing but also paves the way for enhanced efficiency and superior product performance. Whether you’re looking to optimize production processes or elevate the performance of your products, QISO® stands ready to revolutionize your approach to composite materials.
Explore the possibilities with QISO® and discover a new era in composite manufacturing efficiency. Join A&P Technology in embracing the future of materials innovation.
Embracing Innovation: The Evolution of Braided Fabrics in Composite Manufacturing
In the fast-paced world of composite materials, advancements are continually reshaping how manufacturers approach the production of high-performance parts. One such innovation making waves is the transition from traditional woven fabrics to braided reinforcements, particularly in the critical +/-45° orientation essential for aerospace components like wings, spars, and stringers.
The Limitations of Traditional Methods
Historically, the aerospace industry has relied on 0°/90° woven prepregs for creating off-axis orientations. While effective, this approach presents several challenges, notably in the inefficiencies of cutting and splicing. Each part requires meticulous kitting and handling to align and splice multiple short pieces, leading to significant material waste—often between 30% to 40%. The process complexity extends to engineering efforts to manage splice locations, additional labor for kitting, and stringent quality checks to ensure proper orientation and alignment of overlapping joints.
Introducing TX-45™: A Paradigm Shift
Enter TX-45™, a braided fabric engineered to revolutionize the layup process for +/-45° plies. Unlike woven fabrics, TX-45™ boasts a continuous 45° architectures that nearly eliminates the need for splices. This seamless design not only streamlines manufacturing by reducing labor and material waste but also enhances overall part quality. With consistent thickness and uniform bond lines, TX-45™ minimizes disruptions in load paths and optimizes structural integrity.
Efficiency Unleashed
The benefits of TX-45™ extend beyond waste reduction and quality improvements. Manufacturers experience up to 40% savings in labor, material usage and significantly lower equipment costs due to simplified handling and processing. The continuous nature of TX-45™ allows for faster layup rates and improved sustainability, aligning with industry demands for efficiency and environmental responsibility.
Transforming Aerospace Manufacturing
In practical terms, TX-45™ facilitates the creation of complex, high-strength parts with ease. Its inherent drapability and uniform tension across both directions make it ideal for shaping intricate geometries without compromising on performance. Whether reducing parasitic weight or enhancing structural reliability, TX-45™ sets a new standard in composite manufacturing, enabling manufacturers to achieve lighter, stronger, and more cost-effective solutions.
Conclusion: Embrace the Future
As aerospace and other industries push boundaries with ever-evolving demands for performance and efficiency, materials like TX-45™ stand as a testament to innovation. By adopting braided fabrics for +/-45° plies, manufacturers not only improve their bottom line but also pave the way for a sustainable future in composite manufacturing. Embrace the shift to TX-45™ and unlock new possibilities in engineering, production, and performance. Join the journey towards a smarter, more efficient tomorrow with advanced braided composite technologies.
A&P’s Overbraiding Capabilities Enable High Rate Production
The 30-foot overbraided Frankenstein demonstrator was designed by NIAR, A&P and Fiber Dynamics to explore more flexible manufacturing of complex composite structures.
A&P Technology Focuses on Inline Inspection of Multi-Layered Preforms to Increase Rate & Quality
A&P Technology was recently awarded an AFWERX SBIR to expedite the development of inline inspection capabilities for braided composite components for hypersonics and military aircraft.
CW Tours A&P Technology
A&P has made a name for itself as a braider, but the depth and breadth of its technical aptitude comes into sharp focus with a peek behind usually closed doors.