Braid allows for the creation of composite parts with an efficient fiber architecture providing composite part manufacturers with a material that is easily handled, has fewer processing steps, and results in less waste compared to alternatives.
Braid Offers A Sustainable Solution
A&P’s team works closely with its customers at the design level to create braided solutions that optimize use of material and manufacture methods, providing cost savings and minimizing waste. By providing net shape and oriented materials, A&P supports its customers’ desire for sustainable, innovative products that enable efficient methods of manufacture.
Braid Is Rate Enabling
Whether it’s a conformable sleeving, off the roll 45° fabric, a unique quasi-isotropic fabric or a net shape preform, A&P’s braided solutions are designed to support the need for efficient, high volume manufacture.
Braid Provides Optimal Performance
By creating braided architectures that follow the load path and provide impact resistance and high fatigue strength, A&P’s products enable superior performance requiring less material usage. See case studies
A&P Offers A Quick Turnaround
A&P prides itself on its ability to listen to the customers’ needs, propose a braided solution, iterate if needed and then produce custom reinforcements in a short period of time. Customization is second nature to us. Let us help optimize your composite application.
BRAID BASICS
Fundamentally, braid is a system of three or more yarns intertwined in such a way that no two yarns are twisted around one another.
In practical terms, braid refers to a family of fabrics continuously woven on the bias.
Braided-fiber architecture resembles a hybrid of filament-wound and woven material. Like filament winding, tubular braid features seamless fiber continuity from end to end of a part. Like woven materials, braided fibers are mechanically interlocked with one another, but because the fibers are also continuous, braid has a natural mechanism that evenly distributes load throughout the structure.
This efficient distribution of load makes braided structures very impact resistant. Since all the fibers in the structure are involved in a loading event, braid absorbs a great deal of energy as it fails. This is why braid is used as fan blade containment in commercial aircraft.
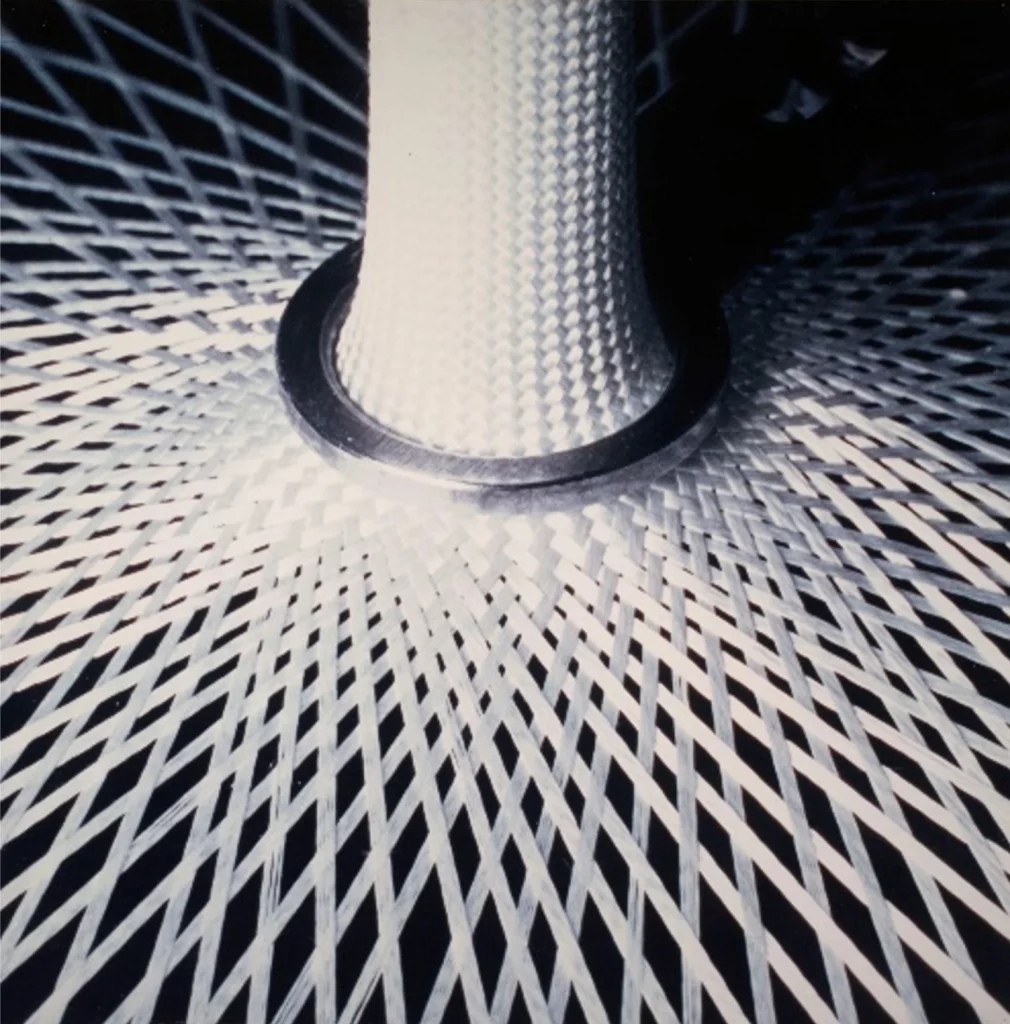
Braids are mechanically interlocked. As a structure is exposed to high fatigue cycles, cracks will propagate through the matrix of filament-wound or unidirectional prepreg laid-up structures. While micro-cracking will occur in a braided structure, the propagation is arrested at the intersections of the reinforcing yarns. This is why braid is the reinforcement choice for aircraft propellers and stator vanes in jet engines.
Braid greatly improves interlaminar shear properties when nested together with other braids. While interlaminar adhesion is no different from other reinforcement products, braided layers move together. As a result, it is very rare for cracks to form and propagate between layers of braided reinforcement. Since braids are woven on the bias, they provide very efficient reinforcement for parts that are subjected to torsional loads. Braid is therefore an ideal reinforcement for drive shafts and other torque transfer components, such as flanged hubs.
Braid sleevings easily and repeatedly expand open to fit over molding tools or cores, accommodating straight, uniform cross-section forms as well as non-linear, irregular cross-section components, much like a sock conforms easily to a foot. This ability to slip onto tools and cores with speed, ease, and a high degree of repeatability, makes braid the ideal solution for products with changing geometries like prosthetics and aircraft ducts.
Virtually any fiber with a reasonable degree of flexibility and surface lubricity can be braided. Typical fibers include aramid, carbon, and fiberglass, as well as various natural and synthetic fibers and thermoplastics. A hybrid braid can also be formed using different raw materials to tailor the ultimate properties and optimize the reinforcement costs.
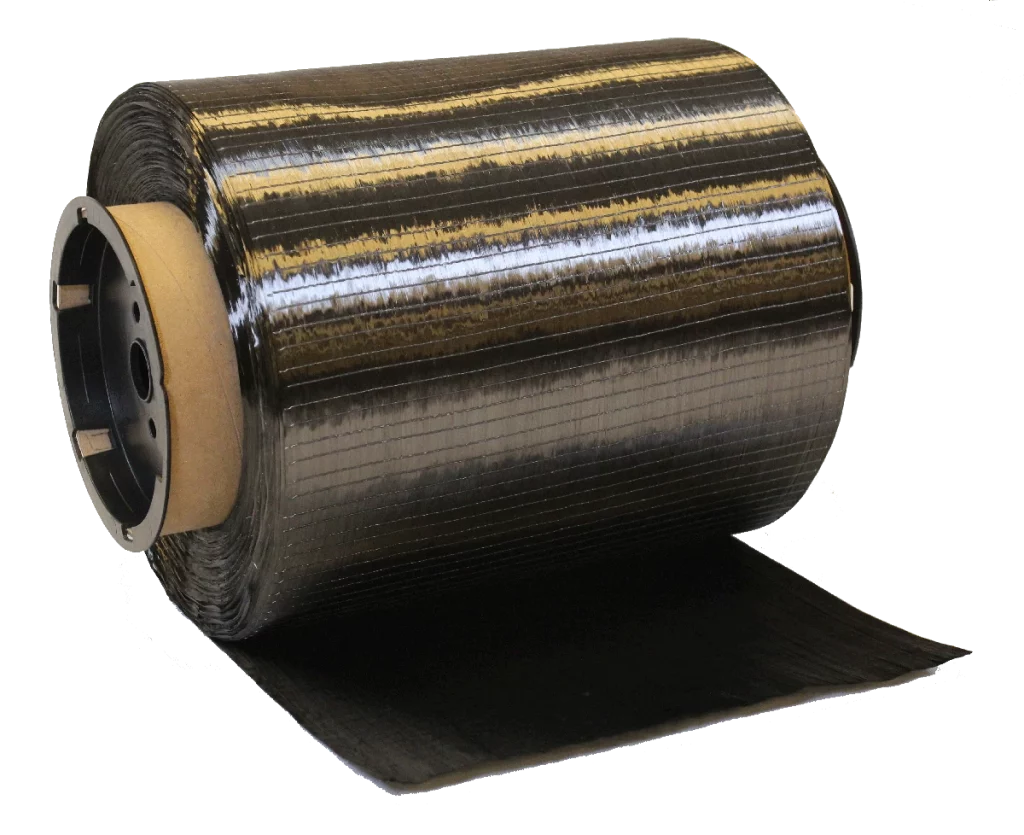
Braid Architectures
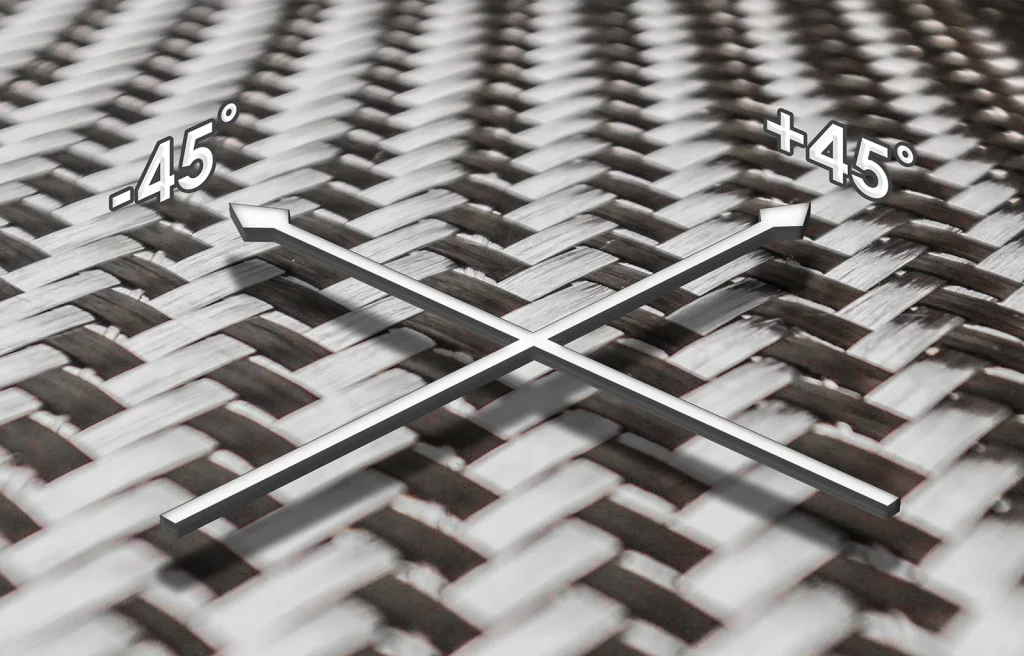
Biaxial
This typical braid construction is most often a basket weave with two yarns crossing over and under each other. Braids are commonly defined at a +/-45° orientation, but are often used at lower angles. When this sleeving is pulled over a mandrel with changing cross-sections the fiber orientation, the thickness, and the yield of the braid vary at each point along the mandrel. These variations are predictable and repeatable and, therefore lend themselves to easy and precise manufacture of composite parts.
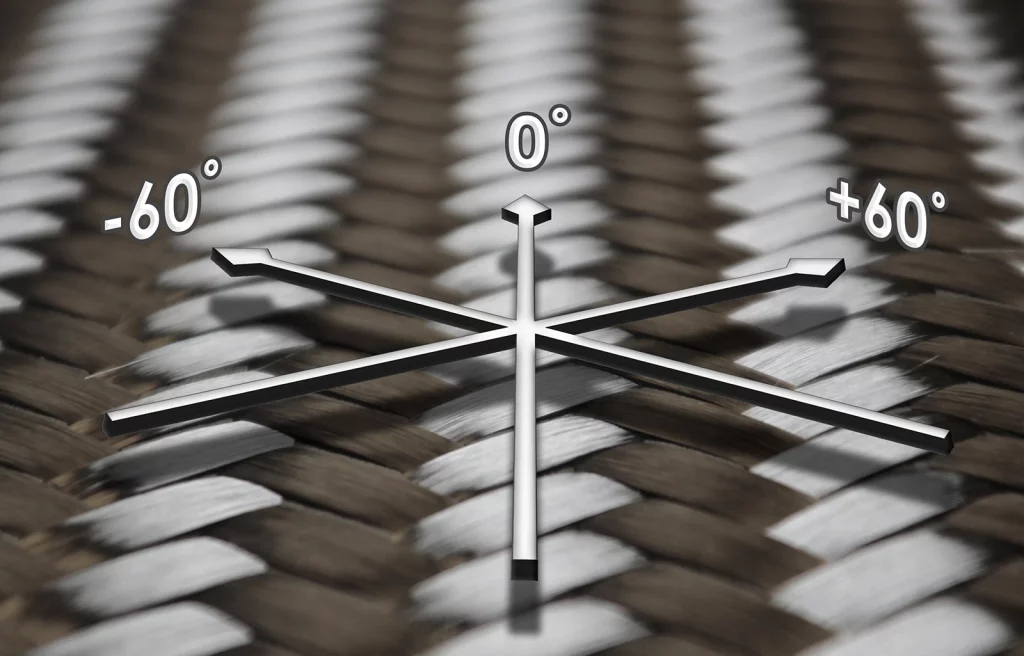
Triaxial
The triaxial form involves adding a third set of yarns in the axial direction. This multi-directional braid achieves unidirectional and off-axis reinforcement within one layer.
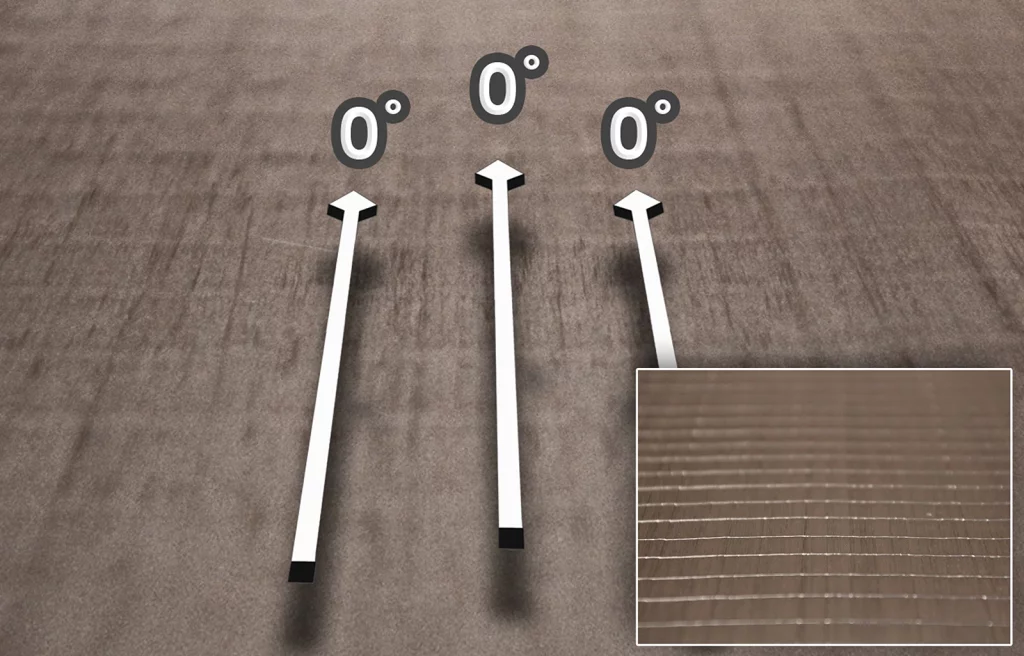
Unidirectional
Unidirectional fabrics are available in a non-woven form providing optimal translation of properties or in a sleeving form in which the bias yarns comprise only 3% of the reinforcement.
Braid Forms
Braided Sleevings
Near net shape, conformable, continuous, available in diameters ranging from 1/4″ to 10 feet in diameter.
Braided Fabrics
Widths available in standard woven sizes with the added advantage of triaxial and quasi-isotropic architectures within a single layer.
Preforms
Net shape preforms create ultimate repeatability for high speed, high volume applications. We can create preforms with the exact dimensions needed for your tool. Contact us at sales@braider.com to learn more.
Overbraids
Overbraiding enables an efficient method of layup onto parts with complex curvatures. Placement of tows using Automated Tape Layup (ATL) is limited by radius of curvature and hand placement of prepreg results in excessive cutting and splicing. A&P Technology’s overbraiding process precisely controls fiber angle providing consistently high part-to-part repeatability.