A good example of braided preforms created to support high volume applications are the braided stator vane preforms produced for Honeywell jet engine exit guide vanes. A&P produces over 30,000 stator vane preforms a year, closing in on the production of a million total.
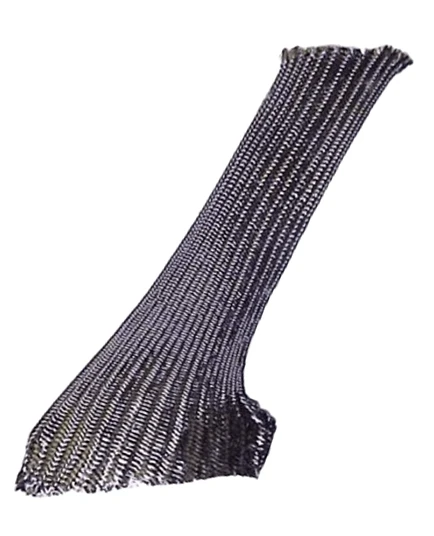
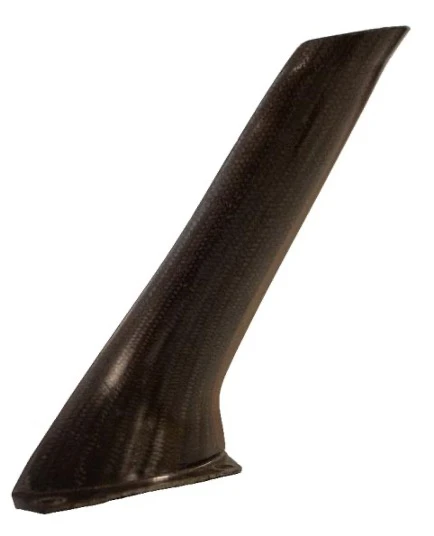
Fan exit guide vanes on turbojet engines are stationary; however, they must endure the pounding of adjacent rotating fan blades while remaining resistant to foreign object damage (FOD). Therefore, precise airfoil shape and high fatigue strength are primary factors in designing and producing stator vanes.
Vanes molded using braided carbon fiber exceed the fatigue and other performance requirements of vanes made with unidirectional carbon prepreg while dramatically reducing part cost. Best of all, braided vanes can be perfectly tailored to the shape of the mold, significantly increasing throughput at the molder.
A&P Technology specially braids the preforms by braiding an aramid preform to shape and then over-braiding the aramid with a carbon fiber shaped sleeve. Braiding angles are precisely controlled to allow for thickness variations in the airfoil shapes. The resulting sleeve, thick in the center portion and thin at the edges, is trimmed to length at A&P Technology. Then, the molder places the preforms in a multi-cavity RTM tool. Once the mold is closed, epoxy resin is injected and cured. The resulting vane is ready for use with only minor trim and deflash operations.