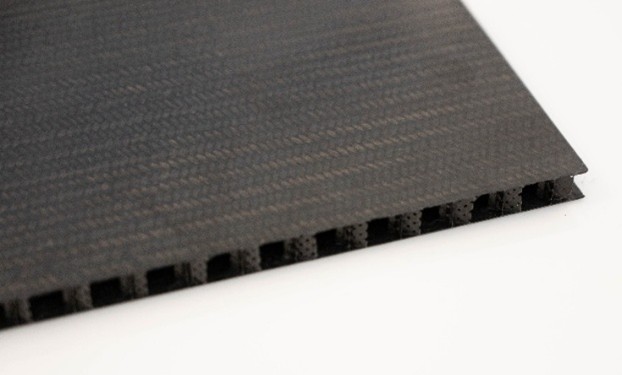
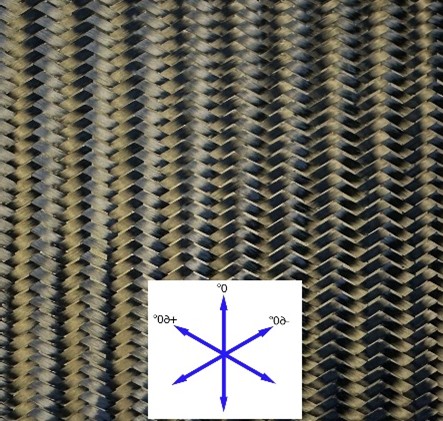
A&P Technology’s high modulus, high coverage HM63 QISO prepregged by Patz Materials and Technologies and used in a single ply on either side of PMT’s Apex low cost vented core, creates an innovative, low-cost solution for high performance space structures. Since QISO is balanced and symmetric in a single layer, 1 ply of QISO can replace 8 plies of unitape needed to build a balanced, symmetric layup – reducing the amount of material needed by half while still meeting strength and stiffness targets.
QISO is a single layer, multiaxial 0°, +/-60° fabric with similar properties in each direction. The in-plane isotropy delivered by QISO provides the mechanical properties needed in a single layer, enabling ease of layup and a significant reduction in weight.
Typically, balanced mechanical properties are achieved in a laminate by performing a multi-ply quasi-isotropic layup; with QISO, cross-plying is not needed and balance is attained with a single ply of QISO. Reduced labor and less material usage equal dramatic cost savings and lightweighting yields a more efficient composite part.
QISO + Apex Core = High Perfomance, Low Cost
The near isotropic mechanical properties of HM63 QISO, shown on the right, combined with the shear performance of Apex Vented Core provides a cutting-edge, cost-effective solution for composite manufacturers looking for rigid, robust, lightweight core.
The carbon fiber and epoxy combination of Apex core resists moisture creating a stable structure in harsh environments.
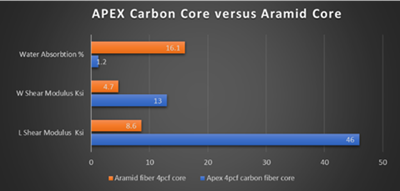
Cost & Manufacturability
Compared to standard carbon core, PMT’s Apex Core is dramatically more affordable than standard core. The low cost of Apex Core coupled with the ease of layup of a single ply of QISO and the corresponding reduction in material usage results in significant cost savings.
HM63 QISO, Apex Core, PMT-F7-AF provides:
- Structural Integrity
- Rigidity
- Low Mass
- Robustness
- Low Cost
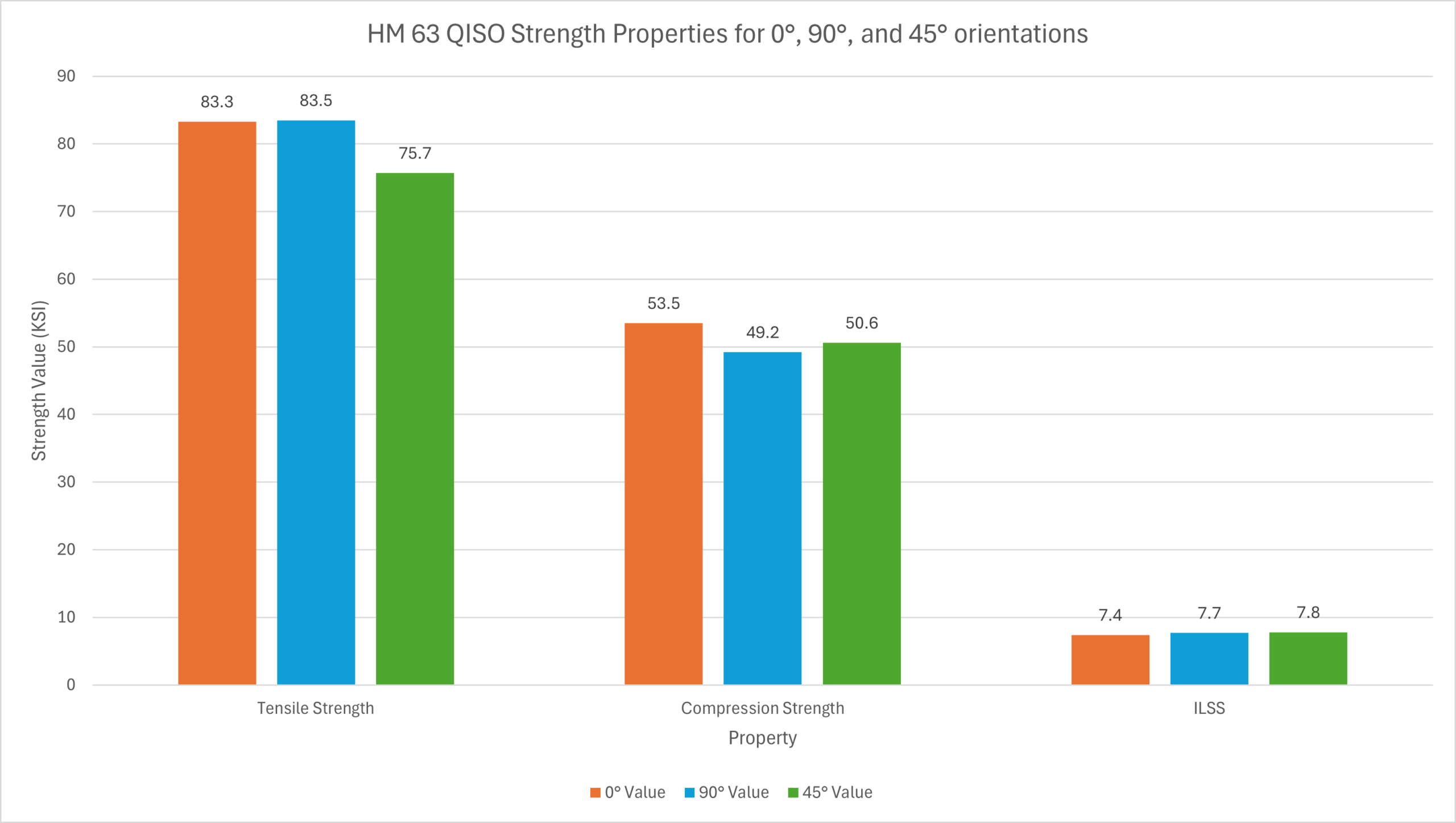
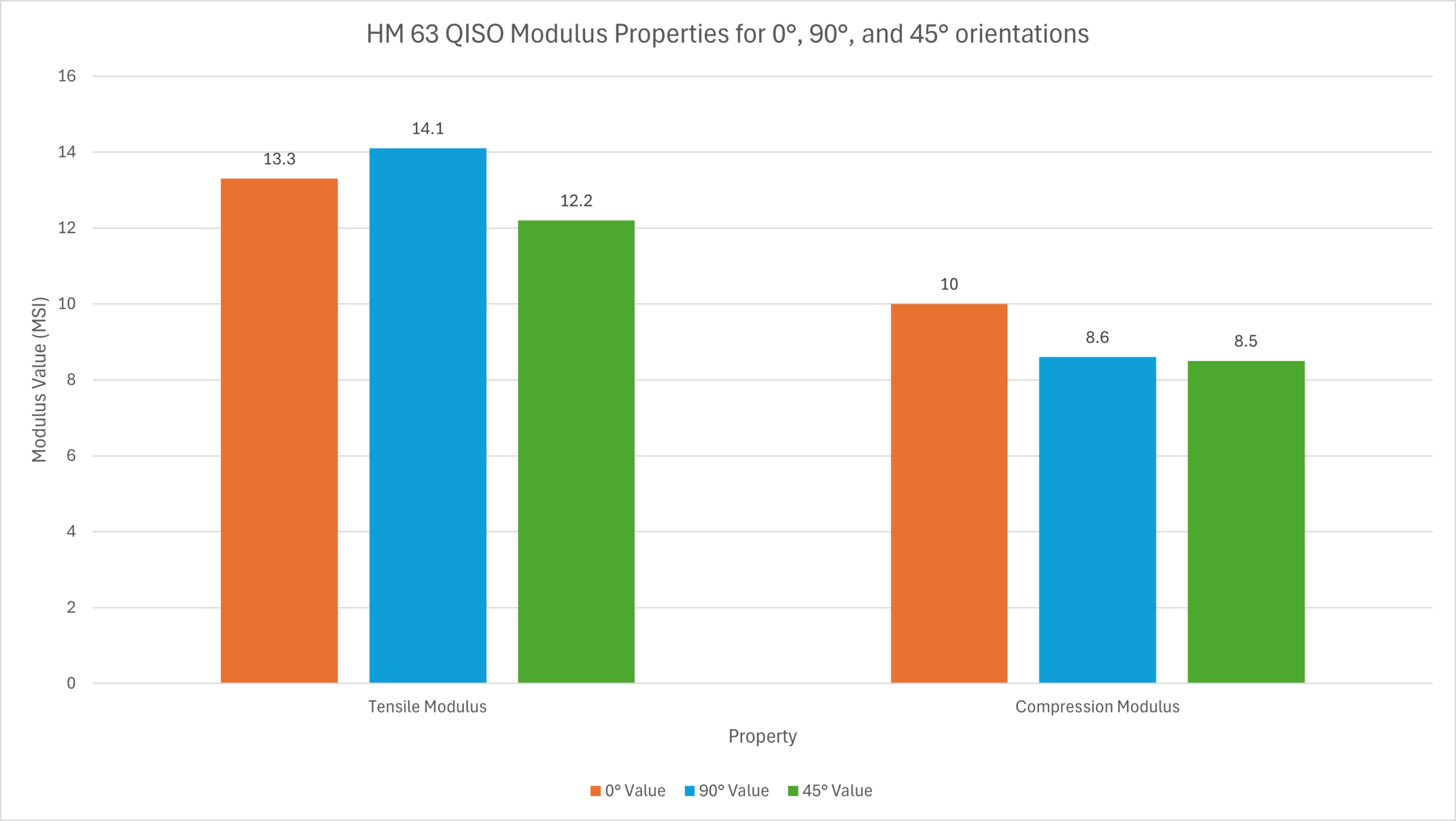